Foam Cementing: Safe or Really Dangerous?
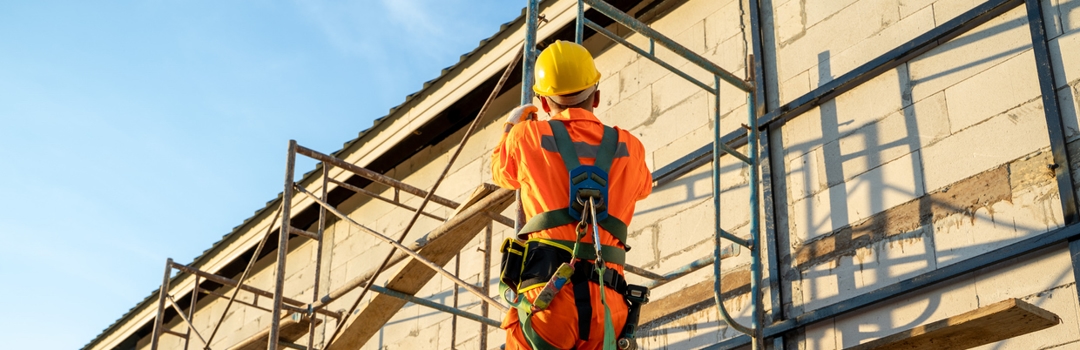
In the complex world of construction and oil extraction, the hunt for materials that combine strength, versatility, and safety is ongoing. Foam cementing technology, used by companies like Halliburton under the brand name "ZoneSeal," represents a significant advancement in this field. Designed to stabilize weak geological formations that are often found when drilling for oil such as shale gas formations or drilling areas near fault zones, foam cementing has become a tool of choice for many in the oil industry. But as with any technology, it brings its own set of challenges and concerns, especially regarding safety and environmental impact.
What is Foam Cementing?
In the complex world of construction and oil extraction, the hunt for materials that combine strength, versatility, and safety is ongoing. Foam cementing technology, used by companies like Halliburton under the brand name "ZoneSeal," represents a significant advancement in this field. Designed to stabilize weak geological formations that are often found when drilling for oil such as shale gas formations or drilling areas near fault zones, foam cementing has become a tool of choice for many in the oil industry. But as with any technology, it brings its own set of challenges and concerns, especially regarding safety and environmental impact.
Types of Foam Cement
Foam cement is categorized into three distinct groups based on function and composition. Understanding the distinctions among these groups is crucial for selecting the appropriate foam cement for a given project, ensuring both efficiency and effectiveness in meeting construction requirements.
Heat-Insulating Foam Cement
Heat-insulating foam cement is primarily designed to provide thermal insulation. It has a lower density compared to its counterparts, which contributes to its excellent thermal resistance properties. It is commonly used to help reduce heat transfer, and therefore effectively improves energy efficiency within buildings. Heat-insulating foam cement is ideal for filling voids, insulating roof decks, and around pipes and ductwork where structural strength is not the primary concern. Its lightweight nature also means it adds minimal load to structures, making it ideal for retrofitting insulation in existing buildings.
Heat-Insulating-Structural Foam Cement
True to its name, heat-insulating-structural foam cement not only provides significant thermal insulation but is also strong enough to contribute to the structural integrity of a building. It is particularly suited for applications where both insulation and structural support are desired without the need for separate materials. Examples include insulated foundation slabs, load-bearing walls with integrated insulation, and floors that require both thermal resistance and the ability to withstand loads.
Constructional Foam Cement
Constructional foam cement offers higher compressive strength and durability than other types; while it still provides some level of thermal insulation, its primary function is structural support. This type of foam cement is used in applications such as load-bearing walls, columns, and beams. Because constructional foam cement is lighter than traditional concrete, it offers benefits such as reduced dead loads, which includes the weight of the building materials themselves and any built-in fixtures or other permanent elements, and potentially lower transportation and handling costs.
Selecting the Right Type
The selection among these three groups of foam cement depends on specific project requirements, including how effectively it insulates a building for comfortable interior temperatures as well as structural needs and overall construction goals. Factors such as climate conditions, building codes, and budget constraints also play critical roles in determining the most suitable type of foam cement.
Applications & Advantages
The applications of foam cement are diverse, and used in various industries. In oil and gas exploration and extraction, foam cementing has become a pivotal technique for securing boreholes and managing the integrity of geological formations. Its ability to adapt to the complex geometries of fractured rock makes it an invaluable tool in this high-stakes environment.
In construction, foam cement is used to produce lightweight, insulating concrete forms. These forms not only reduce the structural load on buildings but also provide enhanced insulation properties. Areas requiring blast-resistant constructions particularly benefit from foam cement's ability to absorb and dissipate energy, making it ideal for military and infrastructure projects aimed at mitigating the effects of explosions.
Safety Concerns & Considerations
It's not enough to recognize the potential of foam cementing; it's critical to understand its interactions, behaviors, and potential risks thoroughly. This understanding necessitates an investment in research, development, and continuous training for those involved in its application.
Foam cement's unique properties—its lightweight nature and enhanced flowability—while advantageous, also contribute to its potential risks. The process of introducing air or nitrogen into cement slurry to create a foam-like substance demands precision and understanding. Any miscalculation in the mixture or handling can lead to instability within the cement structure, potentially compromising the integrity of construction projects or oil wells.
Despite its innovative applications and significant benefits in the construction and oil extraction industries, foam cement introduces a complex array of safety concerns and environmental considerations.
The Deepwater Horizon Incident
The Deepwater Horizon explosion, which occurred in April 2010, stands as a somber milestone in the history of oil extraction, highlighting the critical importance of safety and reliability in the use of advanced materials such as foam cementing. This catastrophic event unfolded in the Gulf of Mexico, where an explosion on the BP-operated Deepwater Horizon oil rig led to one of the most devastating environmental disasters in recent history. Eleven lives were lost, and the subsequent oil spill severely impacted marine life, ecosystems, and the local economy.
The incident brought to light the potential risks associated with foam cementing. Investigations revealed that the cement mixture used to seal the well bore was found to be unstable weeks before the fatal explosion.
Foam cementing is designed to offer several advantages over traditional cement in specific applications, including improved flowability and reduced weight, which can be critical in deepwater drilling operations. In the case of the Deepwater Horizon, the failure of the cement barrier allowed hydrocarbons to enter the well bore, leading to the gas surge that caused the explosion. This failure pointed to a need for rigorous testing protocols, transparent communication among parties involved, and the implementation of fail-safes to address known risks.
The Hertfordshire Explosion
In August 2009, an explosion rocked a construction site in Mill Green, Hertfordshire. In this incident, foam concrete containing incinerator bottom ash (IBA) injured two workers. These incidents often result from chemical reactions within the material or from the material's interaction with environmental factors. In this case, the combination of foam cement and IBA was later found to have produced hydrogen gas, which is highly flammable yet colorless, odorless, and tasteless.
This explosion in particular caused at least two contractors to ban the use of foam cement at their construction sites.
Key Points for Workers & Companies
Both workers on the ground and companies at the helm must navigate the complexities of foam cement with vigilance and informed caution.
For Workers: Knowledge, Training, and Preparedness
Workers involved in foam cementing processes play an integral role in its safe application. Essential points for workers include:
- Comprehensive Training: Beyond basic handling techniques, training programs should encompass the specific properties of foam cement, including its behavior under various conditions and the correct response to potential failures or anomalies. This training must be ongoing, adapting to new insights and technologies in the field.
- Awareness of Material Behavior: Workers should be educated about the signs of instability within foam cement and the factors that could compromise its integrity. This awareness is critical in early detection and mitigation of potential issues.
- Emergency Preparedness: Equipped with knowledge on emergency protocols, workers can act swiftly and effectively should a situation arise, minimizing risks to themselves and the project at large.
For Companies: Quality Control, Communication, and Innovation
Companies employing foam cementing technology bear responsibility in ensuring its safe and effective use. Key considerations for companies include:
- Rigorous Quality Control Measures: Implementing stringent quality control protocols is non-negotiable. This includes thorough testing of foam cement mixtures for stability and suitability for each specific application, with a clear understanding of the geological and environmental conditions at play.
- Transparent Communication: Clear and open communication channels among all parties involved in foam cementing operations— from the field workers to the project managers and external stakeholders— are essential. Transparency regarding material properties, potential risks, and safety protocols can significantly enhance collaborative efforts towards safety and efficiency.
- Commitment to Research and Development: Investing in R&D is crucial for advancing foam cementing technology, improving its safety profile, and expanding its applications. Companies should actively seek out innovations that can reduce risks and enhance the material’s performance.
- Environmental Stewardship: Beyond immediate project concerns, companies must consider the environmental impact of foam cementing practices. This includes careful management of materials and adherence to environmental regulations, ensuring that projects contribute positively to sustainable development goals.
The Future of Foam Cementing
As technology advances, so too will the applications and safety protocols for foam cement. Its ability to be applied underwater, its strength comparable to traditional concrete, and its versatility across industries from oil and gas to construction, make it a valuable material. However, its potential dangers, particularly if improperly mixed or applied, necessitate ongoing research, development, and training.
Despite its numerous advantages, foam cementing is not without its challenges and potential risks. The lessons learned from incidents like the Deepwater Horizon disaster and the explosion in Hertfordshire remind us of the need for vigilance, rigorous testing, and comprehensive worker training. As the industry moves forward, balancing these elements will be crucial in harnessing the full potential of foam cementing while ensuring the safety of workers and the environment.