Underwater & Hyperbaric Welding: What You Need to Know
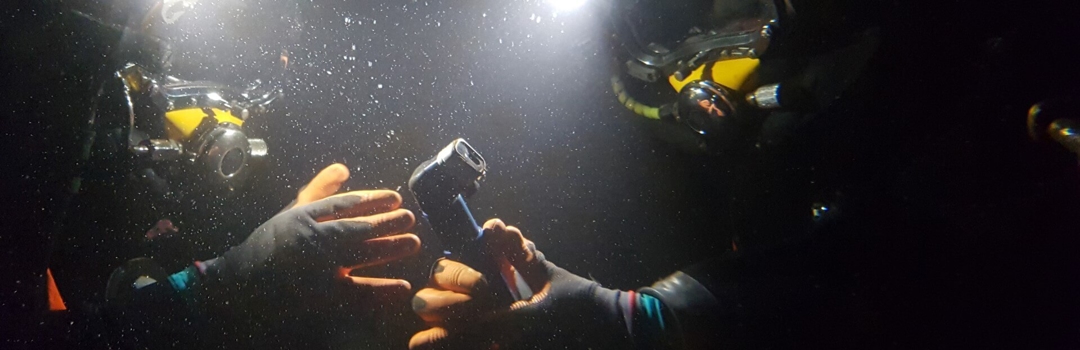
As dangerous as any occupation on an oil rig is, have you thought of the jobs that require people to plunge into the ocean below the rig to keep things running? When a platform structure needs to be inspected, or a pipeline hundreds of feet below the surface needs to be repaired, companies call in an underwater welder.
We need underwater welders, or welder-divers, to help keep hundreds of oil rigs operational and procuring the fuel that makes our world go round. We also need them to keep our dams, bridges, and other infrastructure in good condition. In this article, we're going to take a look at the work of an underwater welder, which is highly specialized, perilous, and often overlooked.
Underwater Welding: A Quick Rundown
In many respects, underwater welding is what it sounds like. A welder gets into a diving suit with specialized gear and then dives up to 300 feet below, or sometimes even 1,000 feet down, to get to work. They have a team behind them too, often a few people on the surface monitoring everything from the power switch (for the electrode) to the diver's body temperature, air supply, and more. This team is typically comprised of backup divers and tenders. A dive tender will help the welder-diver get into their suit, and then will go down below with the welder-diver to monitor and assist from there. This also allows the dive tender to gain invaluable experience to one day work as a welder-diver themselves.
What are some of the items that help a welder-diver do their job?
- Electrode - The tool that makes a commercial diver a welder-diver, it is waterproof when wet welding is called for
- Diving knife - This has many uses, and can be invaluable in an emergency to cut through tangled lines, pry doors open, etc.
- Camera - Needed for inspections
- Diving rope - Particularly useful for certain jobs such as salvage work, cutting, etc.
- Gas panel - Lets the surface team monitor the diver's air supply
- Bailout gas - A backup air supply system in case of equipment failure
- Lighting - Visibility is severely limited underwater, so helmets are generally equipped with a light, and a backup lighting source is a good idea too
The welder-diver is attached to umbilical cords that reach up to the surface and pump in the air needed to breathe, often a gas mixture that includes helium. This helium reduces the concentration of nitrogen and oxygen in that air, balancing out the air to prevent foggy thinking and decompression sickness (more on that later). Communication lines also let the welder-diver update the surface team throughout the job, which includes telling the surface team when to flip their knife switch to power the diver's electrode, and when the team needs to cut off the power.
Depending on whether they work on inland projects, like dams, bridges, and sewer lines, or on offshore jobs, such as for oil rig platforms and pipelines, the underwater welder often does more than just welding and cutting. They are often relied on to provide inspections, do salvage work, and more. According to the U.S. Bureau of Labor, there were about 3,860 such commercial divers as of 2022.
There are a few different paths to this career, but typically a welder-diver will have their high school diploma or GED, a welding certification, a commercial diving certification, and some experience in both welding and diving. Depending on how much experience and training someone has when they decide to pursue this line of work, it can take a couple years or several to reach the position of a welder-diver.
Wet Welding
An underwater welder is typically going to use wet welds. While they can be a challenge to pull off, they're more cost-effective than dry welds.
It takes a great deal of skill and experience to perform a professional welding job while swaying deep underwater, where gravity works differently. It's also difficult to see what you're doing. Once the waterproof electrode is powered on, it produces an electric arc that shields the site that's being worked on with vaporized water. This also creates a lot of bubbles, obscuring a welder-diver's vision even further. It's challenging, but generally more cost-effective than dry welds
Dry Welding / Hyperbaric Welding
Though wet welds get the job done, a dry weld is going to be even more precise. It requires even more specialized equipment, however, equipment that can usually only be used for one specific site at a time and never reused. For some projects, it's worth it.
In larger hyperbaric welding projects, an entire habitat is constructed to cover the work site, perhaps a section of pipeline. The habitat expels water, fans out gases, and filters in new air. The welder dives down to this habitat, and upon entering, can take off the diving helmet and put on a welding hood instead, able to breathe the hyperbaric chamber's air while deep underwater. There they can weld much like they would on land, at least with far greater visibility and control than they could in the water. They then put their diving helmet back on to (carefully and slowly) re-ascend to the surface when the workday is done, where there will be access to a decompression chamber if needed. These pressurized chambers help divers breathe in more oxygen than is available in the outside air while reducing and eliminating nitrogen bubbles in the blood and tissues. Such large hyperbaric chamber projects are rare, however.
A dry weld may instead involve a much smaller chamber that covers just the welder-diver's head and shoulders as well as the immediate worksite, enabling them to still perform a dry weld at a specific area. An even smaller habitat may house just the site itself, and the welder-diver will have to get their electrode inside the small enclosure to perform the spot weld, while they themselves are still entirely in the water.
Saturation Diving & Welding
Normally, if you just dive down deep to get to work hundreds of feet down, you have a more limited time to actually be performing the work needed, since the ascent up and decompression afterwards can take up a significant portion of the day, a necessary precaution to avoid getting decompression sickness (also known as the bends). When you live at pressure, however, you can be doing work for the full shift.
This type of commercial diving and welding work is known as saturation diving. It requires the divers to live in a hyperbaric chamber for weeks at a time in order to stay at the pressure at which they'll be working while out in the water, even though the chamber itself is not very far from the surface. The chamber can be about 9 by 20 feet, a fairly cramped space to be sleeping, eating, and showering in, but about two to four people will get in there. The hyperbaric chamber then gets pumped with a gas mixture that includes helium, slowly pressurizing the chamber over the course of up to several hours. It can get quite cold, and the pressure takes a toll on the divers' joints. Food and personal items get sent down a small airlock, with the divers needing lots of vitamin D supplements and about 6,000 calories a day to keep up with the demanding work. Dirty clothes get sent up. Simple tasks like flushing the toilet are a complex, two-person job. A larger airlock is used to send down the dive suits.
When it's time to work, the underwater welders get into a pressurized diving bell that's attached to the chamber, and a crane can take the diving bell down to the depths where the welders will work. They then get out of the diving bell to work in the water for about six-hour shifts, which can involve assembly, repair, disassembly, welding, or more. Then it's back to the pressurized diving bell and then the hyperbaric chamber. Once the weeks of work are up, the saturation divers will have to spend days in the chamber as it depressurizes. While they have electricity and comms the whole time, there's no work to distract them while they just wait in the claustrophobic space before they can finally step outside and on land.
Out of the thousands of commercial divers in the industry, only a few hundred perform this type of specialized, harrowing work.
Underwater Welding Inland vs. Offshore
While welder-divers are invaluable for offshore oil rigs, they're needed closer to home for work in lakes and rivers as well. From docks and bridges to ships and sewer pipes, underwater welders are needed for installations, inspections, repairs, and more. With inland work, welder-divers usually go home at night and commute to work each day, working a standard 40 hours a week under the water, though seasons that demand extensive repairs could mean they work 20 to 30 hours of overtime each week. An underwater welder working inland can expect to work about 175 hours a month.
Offshore welder-divers may need to inspect, repair, and spot-weld pipelines; plug and clap wells; inspect chain anchor legs; install, repair, or salvage platform structures; or do work on navy ship hulls or cruise lines. They may be working underwater for 40 to 80 hours a week, and these welder-divers keep up the pace for about four to six weeks straight before taking a week off, or maybe two weeks, back on shore. Overtime is normal, meaning shifts can easily last 10 or more hours a day, adding up to 240 hours or so each month. This may not include the time spent in decompression chambers to avoid decompression sickness as needed. This grueling pace can usually last for nine months or so, as weather conditions between December and March prohibit this type of work.
Now offshore welding jobs might boast that welder-divers can be earning up to $300,000, but that's not a realistic expectation. The average salary of an underwater welder is $54,000. This means that there are underwater welders making around $30,000 or less, though this may perhaps reflect seasonal work, and not a full year's income. Offshore work does pay considerably more than inland jobs would, but you likely have to be at the top of the field to make $100,000 or more. That said, many welder-divers do make a pretty penny, which keeps them at these hazardous jobs.
How Dangerous Is Underwater Welding?
Underwater welding, especially offshore, combines the hazardous worksites of commercial diving, construction, and offshore oil rigs into one. Unfortunately, this does not mean that regulations and oversight are increased. Up-to-date statistics on fatalities and injuries are also suspiciously lacking.
Even so, the last time OSHA provided hard numbers on this, the CDC determined that commercial divers' fatality rate is 40% higher than that of any other workers.
Here's what else we know. An older study found that between 1968 and 1978, about nine hundred underwater welders perished in the Gulf of Mexico. This staggering number was somehow attributed mostly to diver inexperience and equipment malfunctions. Based on CDC data from 1989 to 1997, on average 11 welder-divers died on the job each year, which may speak to improved technologies, but perhaps underreporting as well.
For more recent numbers, a diving supervisor was able to find data from 2002 to 2014, and she found that on average, the age of underwater welders when they died on the job was 37 years old. An underwater welder in their mid to late 30s is not inexperienced by that point, which undermines one of the main ways that companies try to blame welder-divers' for their own deaths. Many suspect that this data points to companies cutting corners on safety procedures and equipment maintenance as well as on investigations.
What Risks Do Underwater Welders Face?
The following risks can apply to inland and offshore welder-divers equally. For both types of work, these risks are not due to inexperience. These commercial divers aren't just adrenaline junkies either; they are willing to take risks, but they do so with an abundance of caution and skill.
Drowning
While your first thought may be that mixing electricity with water is a primary hazard (and it is in fact not ideal), one of the main dangers that welder-divers face is drowning. This is mostly because when things go wrong in this job, they can quickly go very wrong. The most immediate danger a diver runs while underwater is that of a damaged or depleted air supply, whatever the ultimate cause of that may be.
An underwater welder's risk of drowning can be caused by:
- Entrapment from equipment
- Cords getting tangled up or breaking
- Air supply failures (whether these hoses get cut or pinched, or malfunction, there are several ways for an air supply to get cut off)
- Heart attack while underwater
- Severe injury to the diver that prevents them from resurfacing before their air runs out
- Delta P, or differential pressure hazards
Delta P (Differential Pressure)
This hazard occurs when a diver is in a low-pressure area of water, and high-pressure water moves in, sometimes the result of a valve pumping out or an intake drawing in water. This creates a powerful suction force, one that applies hundreds of pounds of force against the commercial diver, trapping them between the two bodies of water until the diver runs out of air and drowns.
If an underwater welder notices this differential pressure once they're in the water, it's too late for them to do anything about it. This is a hazard that should be noted before a welder-diver enters the water, as areas of water should be inspected (with remote technology) ahead of time and the pressure calculated, with proper lockout/tagout procedures followed to the letter for valves, gates, etc. This is a detectable and preventable hazard, even though it isn't visible to the human eye.
Even so, Delta P is said to be the cause of two out of every three commercial diving deaths.
Nitrogen Narcosis
This is the reason that underwater divers breathe a gas mixture that includes helium. If a welder-diver breathes in too much nitrogen, then this can induce feelings of euphoria that have been compared to drinking too much alcohol. Impaired mental abilities can be fatal when you're already in such a high-risk situation. Nitrogen narcosis can also cause a sense of numbness, which can inhibit a diver's body from sending warning signals to the brain that the water has grown dangerously cold. Welder-divers have also reported suffering convulsions and hallucinations from this, which is not great in deep water while wielding dangerous tools. More seriously, however, it can also create dangerous mental fog and even cause a diver to lose consciousness. Resurfacing can quickly fix this problem, so all is well if the backup team is able to get the welder-diver above water again. The main danger can come from before then, when the underwater welder is acting and making decisions while mentally impaired.
Explosions
Welding can produce temperatures of 10,000° Fahrenheit or hotter, enough to split up hydrogen from oxygen in the water. If hydrogen builds up, and especially if fumes or gases from the oil rig or another worksite are added to this buildup, the electrode can quickly set off an explosion. in fact, explosions accounted for 7% of underwater welding deaths from 2014-2015.
Other Dangers That Welder-Divers Face
- Decompression sickness / barotrauma / the bends - Nitrogen bubbles in the blood and tissues that can cause cramps, nausea, paralysis, and death
- Arterial gas embolism - Gas bubbles that cut off blood to the heart, lungs, or brain, which can result from decompression sickness
- Hypothermia - Sometimes an insulated suit can't compensate for the cold water, and even mild hypothermia can impair a diver's all-important reflexes and mental processes
- Electrical shock
- Strong currents/rough water
- Falling equipment - This can trap, crush, or severely injure divers
- Hearing and eyesight damage
- Oxygen toxicity - Which can bring on flashing lights in the eye, tunnel vision, ringing ears, lethargy, nausea, vertigo, numbness, convulsions
- Sea life - Jellyfish, stingrays, sharks, etc., especially if a current pulls a welder away from a safe area
What Is the Life Expectancy of a Welder-Diver?
Typically, 10 to 15 years on the job. This may not factor in people simply leaving the job, since such physically demanding work can only be kept up for so long, especially if it takes you away from home for months at a time. However, there is a nearly 15% fatality rate in this field. While the Bureau of Labor Statistics doesn't give out fatality rates for this occupation, the consistent number given is 11 underwater divers still die each year. This also doesn't address data on trainees who die during diving school, nor are injury rates addressed.
Who Is Responsible for Underwater Welders' Safety?
There are industry regulations for welding, construction, oil rigs, and other types of work that can also apply to underwater welders. Certain state laws may cover inland welder-divers. OSHA has some regulations specific to commercial diving, such as an employer's responsibility to check a diver's well-being after ascending and providing a decompression chamber. However, investigations and enforcement seem to be another matter, one that doesn't seem to have much in the way of resources put behind it.
When you're doing construction work underwater, especially when it's in the depths of the ocean, there are many hazards involved. But many of the risks that end up being an underwater welder's demise are thoroughly preventable. Equipment failures can be avoided by regular inspections and maintenance, Delta P hazards are discoverable before someone dives in, and stricter physicals could ensure that only thoroughly healthy people are sent into the water. The reality is that underwater welders depend on the team they work with and the companies they work for to create careful diving plans and follow safety measures.
If a supervisor or company fails at any point in their duty to ensure an underwater welder's safety, it shouldn't be up to the welder-divers' families to spend their own time and other resources trying to figure out what happened. Unfortunately, that's often how it turns out, as government agencies aren't keeping track of recent injury or death rates for this profession, much less following up on a company's inadequate investigation into a fatality. Reported deaths are often written off as another drowning accident, without getting to the root of the cause and how to prevent such disasters in the future. Without pressure from outside sources, companies that employ underwater welders may continue to be slow to improve safety measures, failing to protect the workers of this vital but hazardous occupation.
- Categories